In 2019, eight companies from Yao that have supported Japanese manufacturing “in the background" took advantage of AWRD's co-creation platform to challenge the world's stage with creators selected by the public. This culminated in the Yaoya Project, a product exhibition event to be held in Taiwan from February 19, 2020.
Yao is located on the east side of central Osaka, and is recognized as a core city with a population of over 200,000 people. For a long time, summer in Yao has been associated with the Yaokawashiondo Festival, which has attracted many visitors from outside the city. What has supported this culture and the way of life of Yao has been the local manufacturing, boasting advanced capabilities in technology and product development.
Before this first foray with the Taiwan debut of the Yaoya Project, I was able to talk with representative director of OTSU Co.,LTD, Mr. Hirotaka Kajihara, who participated as a business operator, as well as Mr. Takaomi Okajima of the planning and development department, and Mr. Kunikazu Hamanishi of Hamanishi DESIGN, selected unanimously by the judges, about changes undergone and plans for the future. We will present the story behind the world-class “Made in Japan” manufacturing quality seen through this project.
Manufacturing starting from a miraculous encounter.
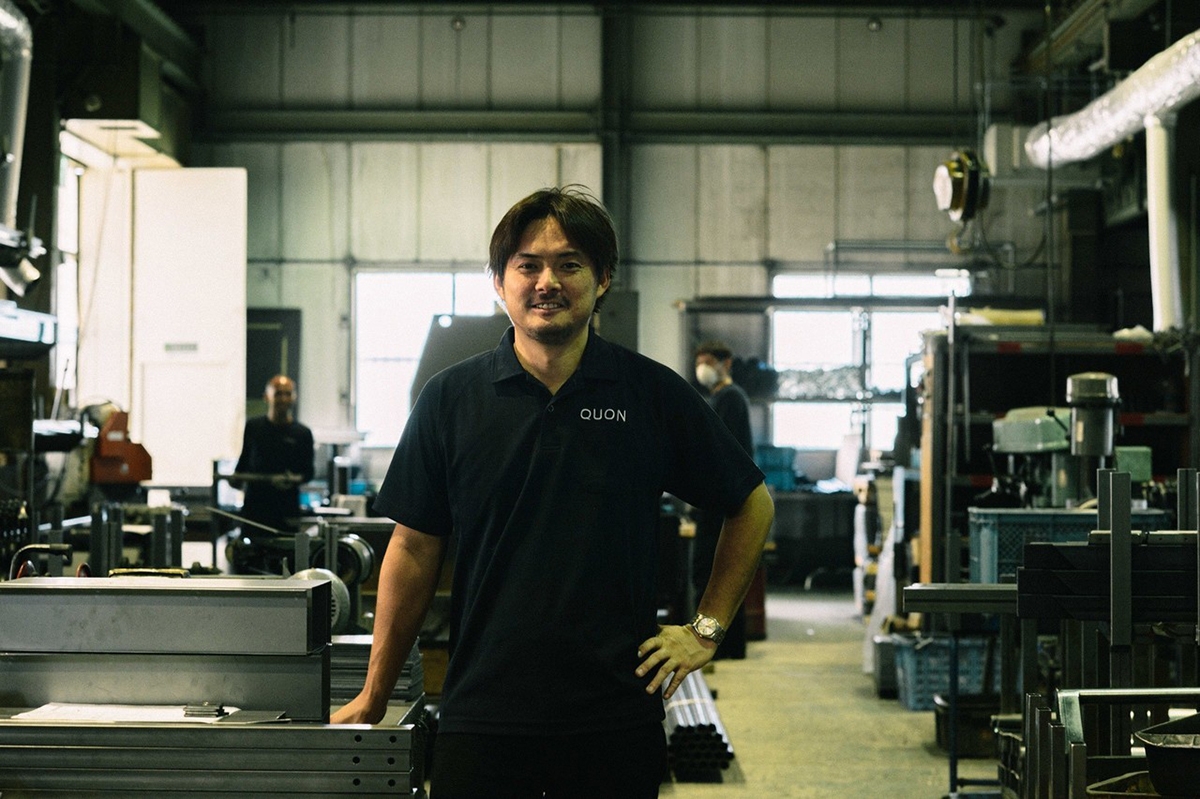
ー(AWRD editorial staff, hereafter omitted): Could I ask, starting with you from OTSU Co., (hereafter Otsu) how it was that you came to participate in the Yaoya Project?
(Representative director of OTSU Co.,LTD, Mr. Hirotaka Kajihara, hereafter Kajihara.)
company manufactures tables and chairs, specializing in B2B. We were founded 58 years ago originally as manufacturers of hardware. Now our forte is creating furniture using steel processing technology for restaurants, leisure facilities, business spaces, as well as contract furniture (furniture for use in business by corporations.)
Up until now our main focus had been on developing domestically, and just when I was vaguely beginning to consider developing overseas, I was told that “there is going to be a manufacturing project in Taiwan with other creators” and I was asked if I wanted to participate. I guess you could call it a timely offer, and I decided that if this was a place to take on a challenge then I would want to participate and take that on.
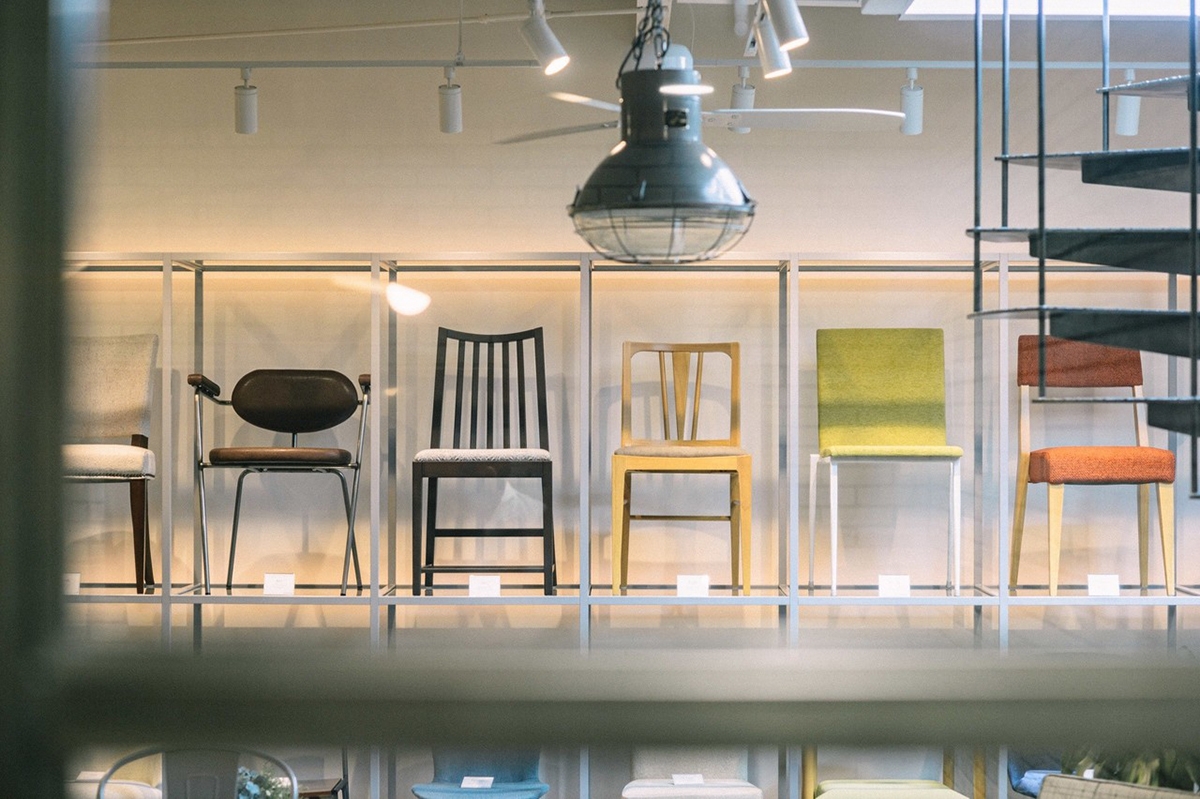
―In the Yaoya Project, product ideas conceived by the public were adopted and were manufactured together with those creators. What made you choose Mr. Hamanishi as the designer?
Kajihara: There were five finalists remaining in the last public screening. Among them was Mr. Hamanishi, and after taking a look at his presentation materials I thought it was interesting how he had used bamboo for the furniture, which is a rare choice. To be honest, I also just thought it seemed like the easiest design to make (laughs).
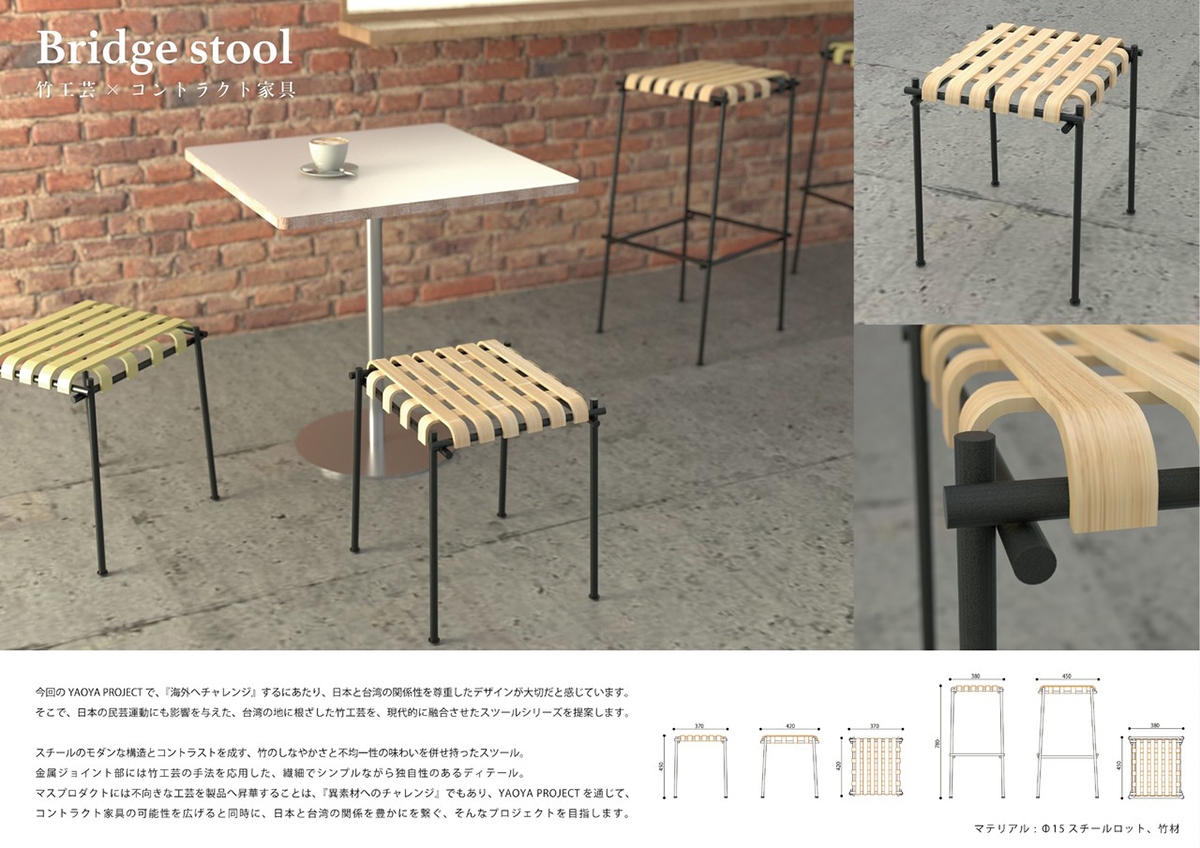
There were many other striking works that caught my eye, but I felt that this design was most in keeping with Otsu. It conveyed to me that he was trying to get a grasp on the Otsu company, the sense of narrative behind our products, and the strengths of our manufacturing. I guess you could say I feel as though I fit with Mr. Hamanishi completely, and so I really think our meeting was miraculous.
―He said yours seemed the “easiest to make” Mr. Hamanishi, can you please tell us about how you got started?
(Designer Kunikazu Hamanishi, hereafter Hamanishi): This is the first time I’m hearing that mine seemed the easiest to make. (laughs)
I used to work at Tanseisha, a “space creation” company, designing the interiors for many restaurants and businesses. To be honest I had already handled Otsu products around that time. At the time I didn’t have very deep knowledge about furniture and so I would search for pieces that would fit the space I was working on from a number of catalogs, and Otsu was one of those manufacturers I took on.
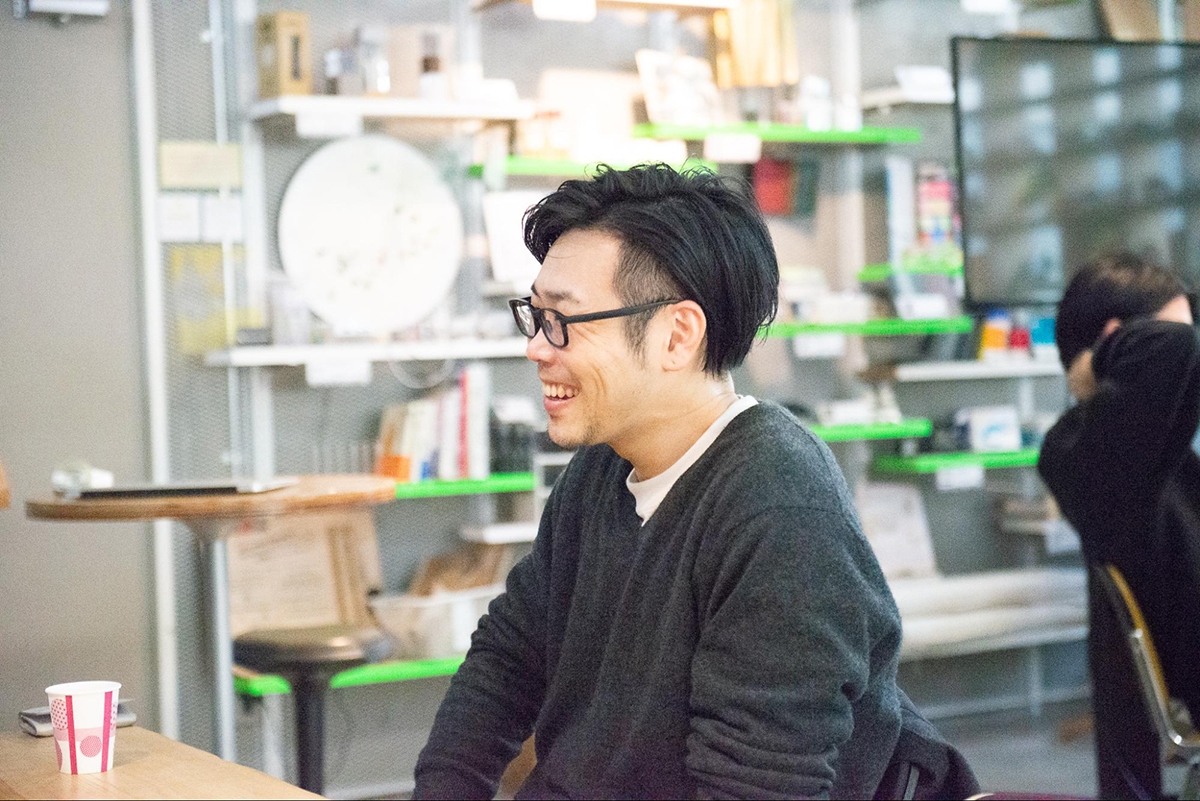
Making up his mind and then taking immediate action, from the Philippines, to Denmark, to Japan.
When I was younger, I experienced living overseas due to my dad’s work, and I thought to myself that one day I wanted to become independent and work globally. With that idea in mind I worked for Tanseisha for seven years, and just before I turned 30, I decided that I wanted to make my dream of independence into a reality. So, without any connections or any future job lined up, I suddenly said “I quit” to my boss, and three days after I had officially left the company, I decided to learn English and went to the Philippines. I thought that I could master English in about three months, but I ended up staying there for a year.
― That’s some amazing vitality!
During that year I was considering my next step and thought that I wanted to design furniture that would match the space it was placed in. I then learned about a course from a vocational school in Denmark in which I could make the furniture I had designed. So, I thought “I’ll go make furniture!” and then spent half a year in Denmark. The workshop of the vocational school ran on a 24-hour system and so it was an environment where I could make the products from my ideas as soon as I put them on paper. I was intently repeating a loop of sketching, creating, and then adjusting. I think my knowledge of furniture increased because of this.
After that, I returned to Japan and set up an office, which was five years ago. Since establishment I have applied for global awards around once or twice a year, went to Italy to present home furniture I designed myself at the “Milano Salone” trade festival, and have actively worked to find places to do business overseas. Then I learned about the “Yaoya Project” through social media. I already knew about Otsu, and given the chance to use my experience in designing business spaces and to take on a challenge with other Japanese businesses overseas, I decided to apply.
A commercial barrier between Japan and Taiwan. Going over there to do business (Hamanishi).
―Bamboo has always been used in Taiwan for everything from building materials to use in everyday items. You designed a stool made of this bamboo, but have you applied any other ideas?
Hamanishi: I have sketched one or two designs, but this piece is the only one I have applied. I have to consider how I can both respect Taiwan’s history and culture while also making contract furniture. Contract furniture demands more strength and durability than household furniture, and I also have to consider possibilities of production volume since I have to make it into an industrial product. And so, after considering nothing but this for about a month, I settled on the most basic bamboo.
Once the idea got approved and I went to the Otsu factory I had an office on the floor above the workshop. I was really touched that I had been provided with an environment where I could give form to my ideas as soon as I settled on them. Mr. Okajima also had a lot of wonderful knowledge about manufacturing, and I felt that I would be able to make something of a very high quality because of this environment and the people I was able to work with.
―After meeting each-other and beginning manufacture, can you tell us about the impressions you had when conducting the field research for your Taiwan debut?
(Planning and Development Department for OTSU Co.,LT, Mr. Takaomi Okajima, hereafter Okajima): When it came to going overseas it didn’t just end with making the products, there were various other things to do with rights and such that had to be done as well. Of course, I learned about Taiwanese culture, but I also learned about design, about how trademark laws are more severe internationally than domestically, and I got a much better grasp on intellectual property. There were a few concepts that I think we were naïve about, so it was a great chance for us to learn new things.
。
Hamanishi: When we went to Taiwan the products were basically decided upon, so I was considering how we should sell them. The truth is that the way distribution works in Taiwan is different to Japan. In Japan we have trading companies that handle products, so if you pay them then they will spread to design companies and so on. In Taiwan however, the architects procure the products directly. We don’t really have wholesale merchants in Japan, so when I went to Taiwan, I was able to meet with a local architect and a key person on the sales floor and just say “Japanese manufacturers want to bring contract furniture into Taiwan. I’m considering this kind of price.” I was doing sales on my own and was able to give a realistic proposal.
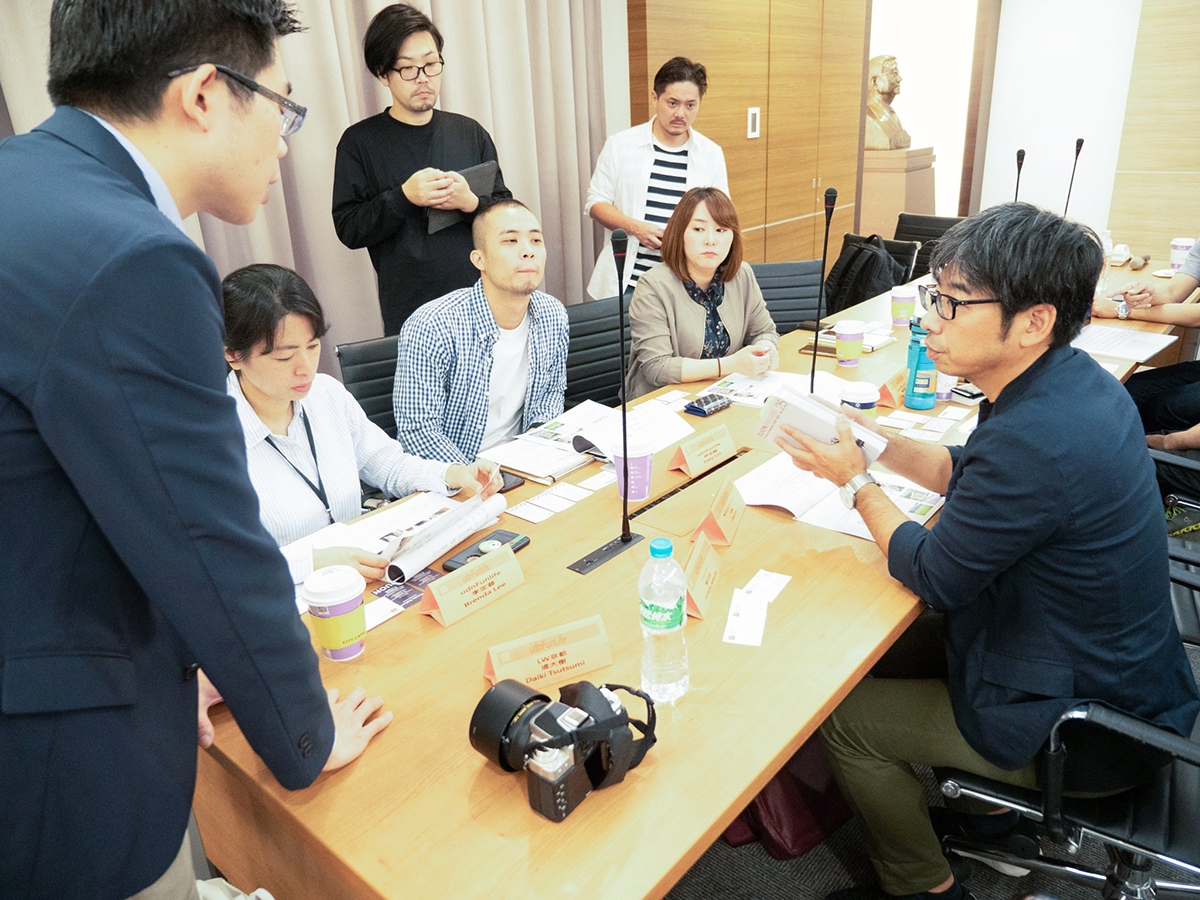
From now on I want us to take on the challenge of informing people about our products and business together, by sharing and spreading our story.
―It’s quite rare for a designer to sell their products themselves. I can feel your enthusiasm for spreading the furniture as a team.
Okajima: This time was like taking on a challenge as a company, and it was a big motivation to try something we had never done before. When we first began some people on the workshop floor would say things like “is this furniture going to be strong enough?” But when I asked them to make the product saying “we have nothing to lose!” the mood shifted to “this is pretty good” and everyone changed their minds. Usually in manufacturing you elect to take the safe route to avoid complaints, but for something like this project we were able to clear away our preconceived notions about manufacturing, and it was an excellent experience for the company as a whole.
―It’s a big affair for the staff to change their mind like that, how did it affect you, director?
Kajihara: Up until now I have worked with many external designers. Back then we would ask them to design the products which would be put in the catalogs, and we would manufacture them. In the case of Mr. Hamanishi, he was saying “consider the future for contract furniture and please think seriously about what manufacturers should do from here on out”, and I was very inspired by that passion.
Okajima: Meeting Mr. Hamanishi really was a big moment. If you only do B2B work, you start to only consider people within your current expectations and don’t really consider making proposals to people in the outside world. Mr. Hamanishi taught me how important it is to make things for general consumers. Of course, I still continued to value the way things had been conducted before, but I also came to think that I wanted to take on challenges which differed from that process. From now on I want us to take on the challenge of informing people about our products and business together, by sharing and spreading our story, and I want those results to reflect on our core business.
Hamanishi: Yes, that’s right. We still have a lot to do to enliven the furniture industry, and I’m looking forward to it.
―We are looking forward to it too! Please tell us if there is anything about this upcoming exhibition in Taiwan that you want to highlight.
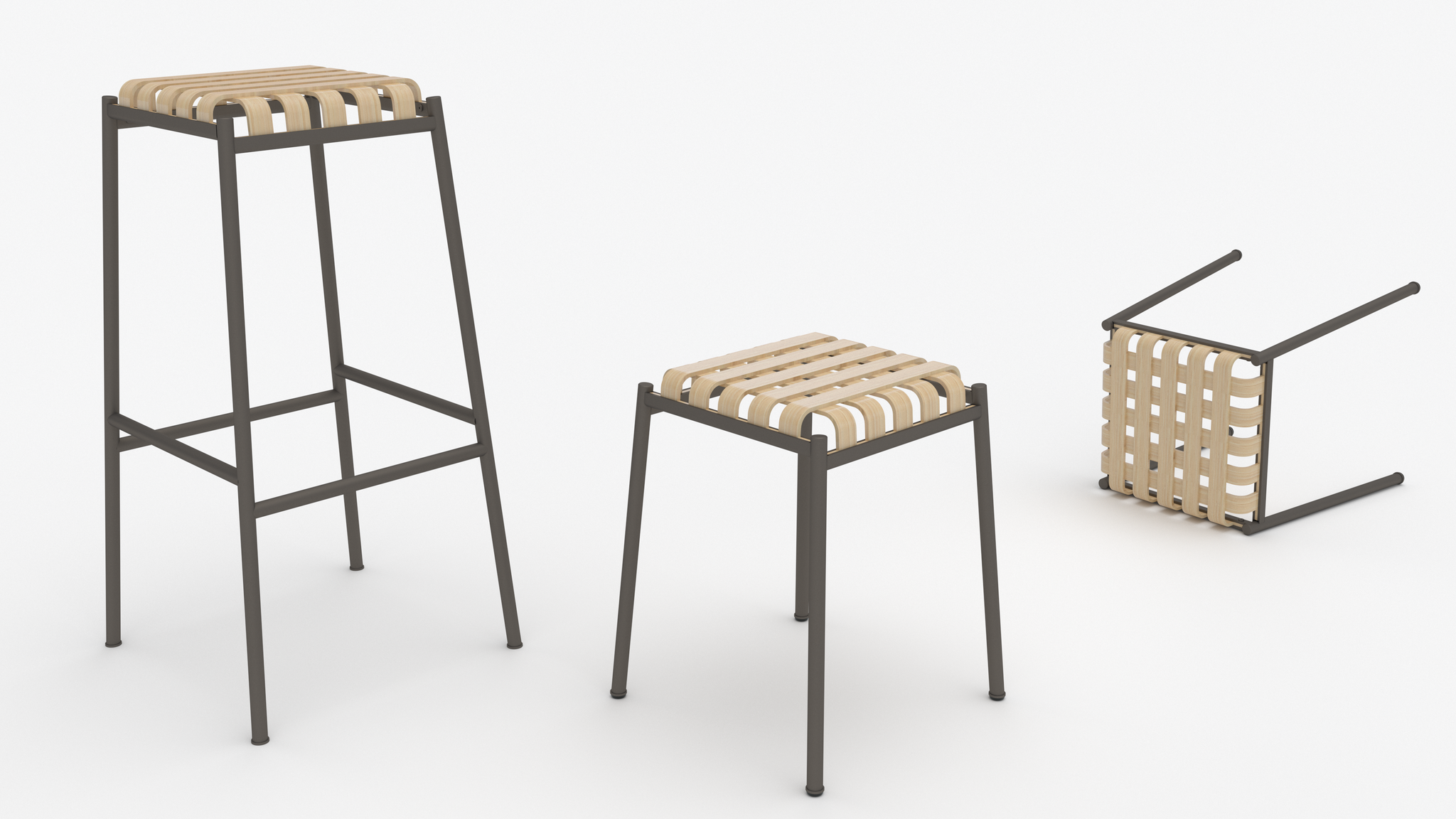
Hamanishi: I think that the highlights are Otsu’s technical abilities, the beauty and accuracy of our welding, and that even using a risky material like bamboo, we have successfully matched the strength and durability that is unique to contract furniture.
The use of natural materials in mass produced furniture is usually disliked from the viewpoint of efficient production. This time we are taking on the challenge of using a material that is sustainable but not really in demand. I think it would be great if what Otsu is creating here will be a reason for the furniture manufacturers of the commercial base to start considering sustainable product development. There is a lot of disposable furniture, but I think this will be a chance to show that it can even be done with contract furniture.
Kajihara: Absolutely! I don’t have anything more to add after that. (laughs)
―We are looking forward to further collaboration between Otsu and Mr. Hamanishi, outside of the Yaoya Project.
Kajihara: Of course, it’s fairly exciting talking about the future. (laughs)
It is our job to increase the quality of products, and so our challenge is to make Hamanishi’s ideas into a reality. Based on our experience in the Yaoya Project, I am hoping to one day do an exhibition at Milano Salone with Otsu and Hamanishi’s brand together. Although it doesn’t have to be in the main venue. (laughs)
Hamanishi: We can do it right away!
■Project information
YAOYA PROJECT:https://awrd.com/award/yaoya-project
■Taiwan Event Information
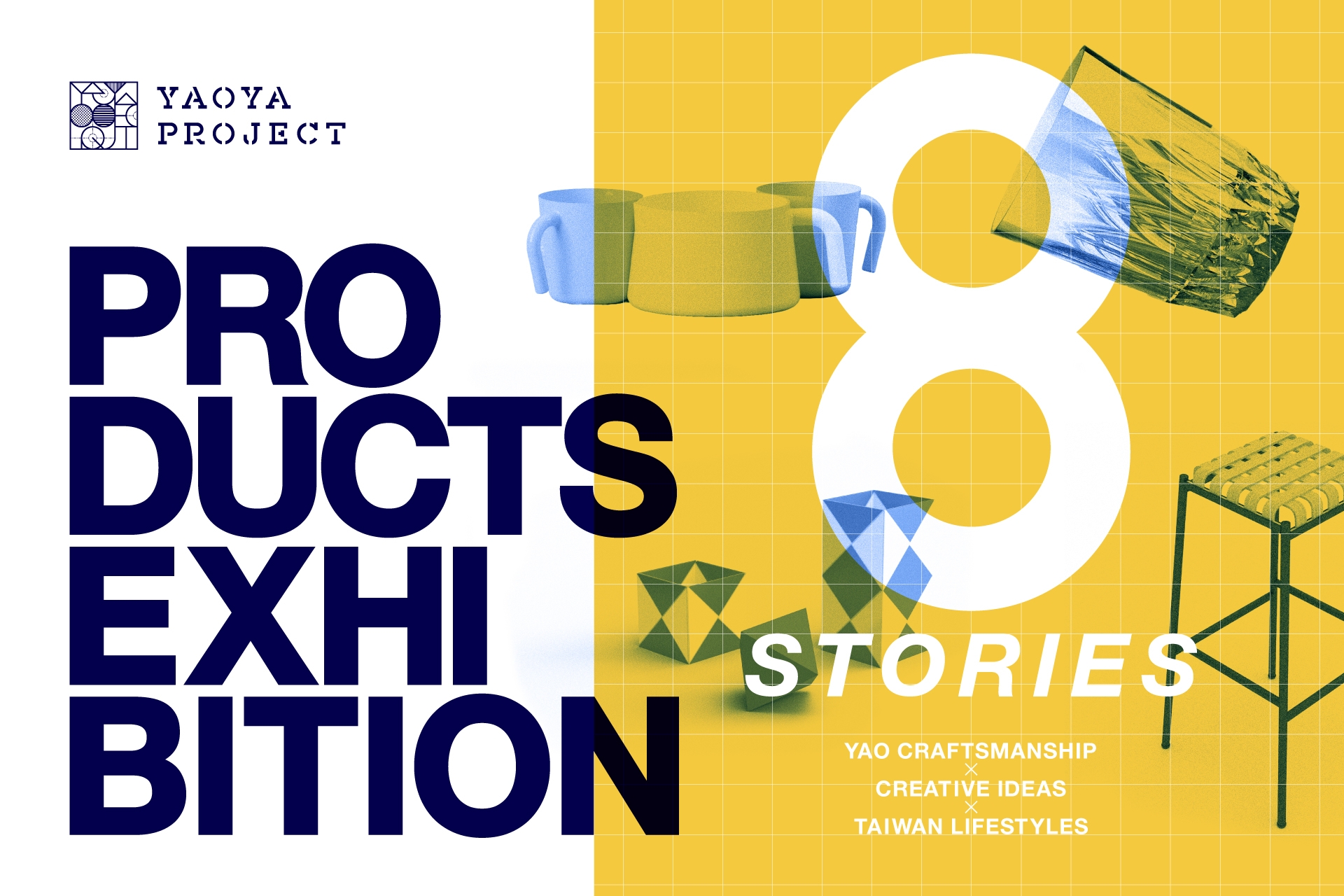
展示名:PRODUCTS EXHIBITION - 8 STORIES -
会期:2020.2.19(wed)〜3.2(mon)
会場:Loftwork Taiwan / FabCafe Taipei
華山 1914 文化產業園區紅磚區西 7-3 館
時間:11:00〜19:00
■OTSU Co.,LTD.:http://otu.co.jp/
A table and chair manufacturer specializing in B2B. Founded as an ironworks, Otsu focused on creating the “trumpet leg chairs” used in pachinko and mahjong parlors and then expanded into making furniture for business use. In addition to their catalog items, they also accept orders and manufacture furniture based on individual designs. Since the launch of their new brand “QUON” in 2011, they have been expanding their field of business around the world.
https://note.com/yaoya_project/n/n01631f2b50ab
■Kunikazu Hamanishi:
Born in Kanagawa prefecture. After graduating from the Department of Environmental Design at Tama Art University, he worked for around seven years as an interior designer for commercial facilities at Tanseisha Co., LTD. Following this, he studied furniture design in Northern Europe (Denmark), and established Hamanishi DESIGN in 2015. Since 2018, he has been appointed as a part-time lecturer at the Nihon Kogakuin College PD department.
Hamanishi DESIGN:http://hamanishi.net/